Overview
The TRUBOLTTM Masonry Anchor was the first of the true dimension anchors to become available to RAMSET Fasteners (Aust.) Pty. Ltd.
The name TRUBOLT is derived from the fact that the diameter of the anchor and thread are the same. This makes the selection of the correct
masonry drill bit very simple, in that the outside diameter (O.D.) of the TRUBOLT anchor determines the hole size
(i.e. HOLE SIZE = BOLT SIZE, 16mm anchor - 16mm drill bit).
With conventional sleeve anchors, the hole size is greater than the anchor bolt to allow for the wrap around sleeve.
TRUBOLTS gained immediate acceptance throughout Europe and are a major seller world wide.
In Australia they have been used extensively in the heavier duty applications that require a greater shear strength on the anchor bolt. A typical
example of this would be the fastening of shelf angles to multi-storey buildings that have an outer skin of brickwork. The shelf angle is usually
a galvanised steel angle, that is bolted to the edge of the concrete at floor level on the outside of the building and is used to carry the brick
façade up the next floor level.
It should be remembered that the expansion principle of the TRUBOLT is very similar to that of the DYNABOLT when relating to Tensile Loads (sometimes referred to as PULL-OUT loads).
Features |
Benefits |
Maximum shear capacity |
Stud diameter equals hole diameter for hole size |
Fast installation |
Through fixing eliminates marking out and repositioning fixtures |
42 micron Hot Dip |
Outstanding exterior durability |
Galvanised coating |
Superior corrosion resistance |
High clamp load |
Stud design ensures pull down on fixture |
Superior strength |
Cold forged steel construction |
Uses
- A TRUBOLT is supplied as a complete anchor, comprising a reduce shank tapered bolt, threaded part way along at the top end.
A specially designed expansion sleeve is pressed home around the tapered end of the bolt and is the same diameter as the O.D. of the bolt.
- A correct sized flat washer and nut are also supplied. TRUBOLTS are manufactured from MEDIUM STRENGTH STEEL
- All components are plated with a passivated gold chromate finish to a minimum 6um (microns) thickness
- TRUBOLTS are manufactured to standard ISO metric dimensions with the relative metric thread size as is designated by the descriptive
part numbering process
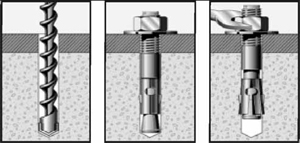
Installation
- Determine the total thickness of the material to be fastened. NOTE: If spencers or shims are to be used add on the thickness
(this is often overlooked and can lead to premature failure of the anchor"s ability to hold). Refer to the ‘Fastens Materials Up To’
recommendation on literature and wall charts.
- This, with the minimum anchor embedment (shown as minimum hole depth) on your point of sale literature, product selection wall chart or your
Ramset Technical Manual, will give you the correct length required.
- A Ramset carbide tipped masonry drill bit equivalent in size to that of the O.D. of the TRUBOLTS being used will be required, for the ideal
drilling system, use a RAMSET DYNADRILL ROTARY HAMMER.
- Drill the hole into the masonry not less than the embedment depth of the TRUBOLT, clean the hole out thoroughly of all chippings and concrete dust,
once more check that the hole depth is sufficiently deep to accept the required embedment of the TRUBOLT.
- Taking the TRUBOLT as a complete assembly, adjust the nut up to flush with the top of the thread, a flat washer should be under the nut,
place the TRUBOLT (sleeved end first) down through the hole in the article to be fastened pressing it as far as it will go. The projecting
segments on the expansion sleeves are known as “Anti-Rotation Lugs” and it is at this time of installation that they become operational.
As the TRUBOLT is being driven down fully into the hole (preferably by tapping with a hand hammer) these projections bite into the sides of
the hole causing the expansion sleeve to be held firmly in one position thus preventing rotation within the hole during expansion.
NOTE: For optimum performance the TRUBOLT must be a tight fit into the hole in the masonry. NEVER install TRUBOLTS into oversize holes.
- After the TRUBOLT has been tapped down fully into the hole, take up the slack by tightening the nut down onto the flat washer which in
turn should be resting against the fixture.
Tighten the nut approximately 3 to 4 full turns with the correct spanner and ensure that the TRUBOLT has been fully expanded. This will be
evident when the nut is tight against the fixture. At the same time the fixture should be pulled down snug against the work surface.
|